داتینگ غبارگیر – اجرای داکتینگ (کانال کشی، نصب هود و سیستم تصفیه هوا مناسب)
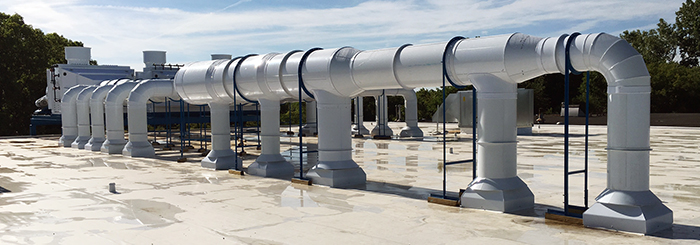
کانالکشی هوا (ductwork) کانال کشی، داکتینگ و تهویه کانالی یکی از اجزا بحرانی و اساسی سیستمهای کنترل آلایندگی هوا است. طراحی داکتینگ در واقع مسیری برای هدایت هوای آلوده به سمت ونت خروجی و سیستمهای تصفیه هوا مانند اسکرابر هوا، غبارگیرهای صنعتی و فیلتراسیون و اسکرابر گاز مناسب هوا است. شرکت ارکان گستر طراح و […]
واحدهای اسید شویی
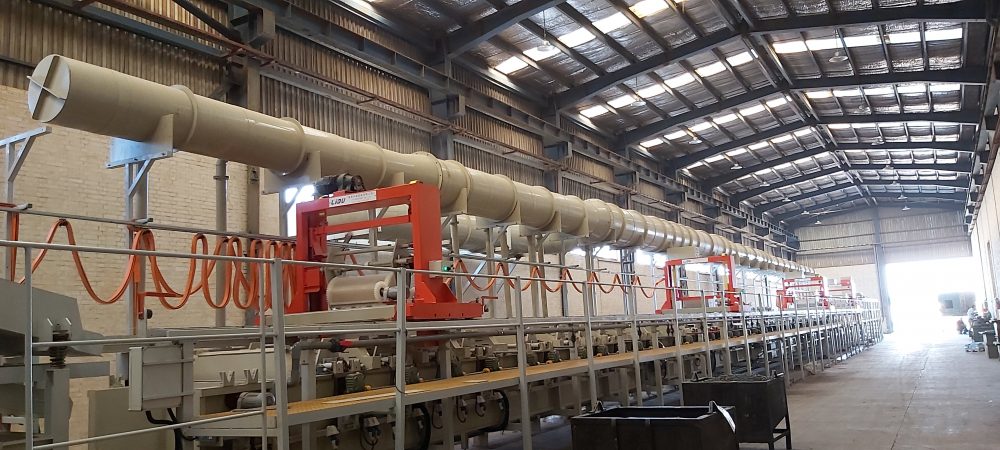
کارخانجات دارای واحد اسیدشویی کارخانههایی که در زمینههای تولید پیچ و مهره، مشتقات اتصالات، تولید شمش روی تولید ورق و …، مشغول به کار و بهرهبرداری میباشند برای تکمیل فرآیند و تولید محصول خود دارای واحدهای اسید شویی یا واحدهای شستشوی اسیدی یا به عبارت دیگر قسمت اسیدشویی washing acid room میباشند. این کارخانجات در […]
واحدهای اسید سولفوریک

فرایند تولید اسید سولفوریک تولید اسید سولفوریک به دو روش سوزاندن سولفور (Sulfur burner) و ذوب فلز (Smelter) میباشد که در کشور ایران با توجه به دسترسی آسان به گوگرد و تهیه سولفور، روش اول کاربرد بسیار دارد. مراحل تولید اسید سولفوریک جریان گازی به همراه خوراک ورودی به فرایند جهت تولید اسید ابتدا وارد […]